News & Technicals
Analyze the Electrode of the Intermediate Frequency Spot Welder
Intermediate frequency spot welders need to be equipped with electrodes to complete the welding work during operation. The quality of the electrodes directly affects the quality of the solder joints. The electrodes are mainly used to transmit current and pressure to the workpiece, but the poor selection of electrode materials will be in the process of use. The medium wear is aggravated, which will increase the grinding time and waste raw materials. Therefore, the electrode should be selected according to the material to be welded.
The electrode must have a certain high temperature hardness, especially at 5000-6000 ℃, the hardness can still be guaranteed, because the higher the high temperature hardness, the less likely the electrode is to pile up during the welding process. Generally, the temperature of the contact between the workpiece and the electrode during welding is about About half of the melting point of the weld metal, if the electrode material has a high hardness at high temperature, but the hardness is low at high temperature, it is still easy to pile up during the welding process.
The working end of the electrode is divided into three types: cylindrical, conical, and spherical. Conical and spherical are the most widely used. They can enhance cooling and reduce the temperature of the electrode. Although the spherical electrode has a long life, fast heat dissipation, and good solder joint appearance, it is manufactured , Especially it is difficult to repair, so conical electrodes are generally used.
The selection of the working surface is related to the pressure. The pressure is large and the working surface needs to be larger to prevent the electrode end surface from being crushed. Therefore, as the plate thickness increases, the diameter of the working surface needs to increase, and the working surface increases due to continuous wear and tear. In welding production, repairs should be made regularly, otherwise the penetration will decrease or there will be no nugget due to the decrease of the current density. The method of automatically increasing the current as the number of solder joints increases can prolong the time between two repairs.
Send Message
Premium Product
Catalogue
News & Technicals
Structure of Nut Electrode of Intermediate Frequency Spot Welder
Analyze the Electrode of the Intermediate Frequency Spot Welder
Analyze the Influence of the Welding Point Distance of the Spot Welder
Function of Butt Welding Machine Inspection System
Contact Us
Email: info@resistancewelder.com
Tel: 0086-185-6889-5678
Factory: No.81 Donghui Second Street, Huangpu District, Guangzhou
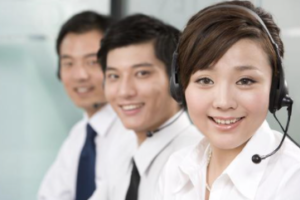