News & Technicals
The Importance of Electrode Grinding for Intermediate Frequency Spot Welding Machine
When the intermediate frequency spot welding machine is working, due to long-term welding, numerous impacts of instantaneous high current and numerous impacts of hundreds of kilograms of pressure, the electrode end surface changes greatly, which will cause poor welding consistency.
During welding, relying on the contact resistance and the internal resistance of the sheet itself, under the action of the instantaneous high current, heat is generated to form a weld nugget, and a weld joint is formed under the later action of the electrode. This requires a large electrode current density at the weld joint, which is several hundred per square millimeter. About ampere, if the welding end face is too large due to loss, it will cause distortion of the welding parameters. Due to the customer’s ignorance, many customers do not often polish the electrode during use, and even extreme customers have not polished the machine after buying the machine. Increasing the welding time and welding current will result in a large solder joint with a large heat-affected zone and poor appearance of the solder joint.
Therefore, during normal welding, try to grind the electrodes as often as possible to ensure the consistency of the solder joints. Cooperating with the electrode dresser of the intermediate frequency spot welding machine can basically guarantee the consistency of the welding point. The common electrode dresser is not manual type. The production line is generally equipped with pneumatic or electric dresser, which greatly improves the welding quality and production efficiency.
Send Message
Premium Product
Catalogue
News & Technicals
Structure of Nut Electrode of Intermediate Frequency Spot Welder
Analyze the Electrode of the Intermediate Frequency Spot Welder
Analyze the Influence of the Welding Point Distance of the Spot Welder
Function of Butt Welding Machine Inspection System
Contact Us
Email: info@resistancewelder.com
Tel: 0086-185-6889-5678
Factory: No.81 Donghui Second Street, Huangpu District, Guangzhou
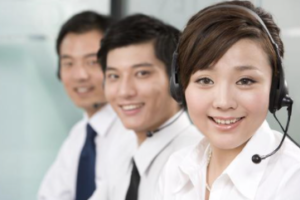